Brick Pointing Material Selection Guide: Making Informed Decisions for Lasting Results
Key Takeaways:
- Material Selection Affects Building Integrity: Choosing the right brick pointing material directly impacts your building's structural integrity, aesthetic value, and maintenance costs, while the wrong choice can accelerate deterioration and damage masonry, particularly in Bronx's climate conditions.
- Compatibility Is Critical: Pointing materials must be compatible with existing masonry in terms of flexibility, strength, and especially permeability. In the Bronx's freeze-thaw climate, materials must allow moisture to escape at appropriate rates to prevent spalling and deterioration.
- Building-Specific Criteria Matter: Effective material selection requires developing criteria specific to your building's age, historical considerations, use case, occupancy factors, and exposure to Bronx's climate conditions including freeze-thaw cycles and urban pollution.
- Installation Quality Determines Success: Even the most appropriate material selection can fail without proper installation techniques, including joint preparation, pre-wetting, mixing, application, tooling, and appropriate curing protocols.
- Documentation Supports Future Maintenance: Thorough documentation of your brick pointing material selection decisions becomes invaluable for future maintenance planning and knowledge transfer between property management teams.
Understanding these principles transforms brick pointing material selection from a technical decision into a strategic one that protects building assets and maintenance budgets for years to come.
When managing properties in the Bronx, few maintenance decisions carry more long-term consequences than brick pointing material selection. The right material protects your building's structural integrity, preserves its aesthetic value, and minimizes future maintenance costs. The wrong choice can accelerate deterioration, damage historical masonry, and lead to costly rework—all while disrupting tenant operations.
Property and facility managers frequently navigate this decision without specialized masonry knowledge, caught between budget constraints and conflicting contractor recommendations. This guide provides a framework for making informed brick pointing material selections specific to your building's needs in the Bronx climate.
You'll develop the knowledge to evaluate options confidently, document decisions effectively, and ensure quality outcomes—without becoming a masonry expert.
By understanding the fundamental principles that govern material performance and compatibility, you'll transform this technical decision into a strategic one that protects both your building assets and maintenance budget for years to come.
Understanding Brick Pointing Material Fundamentals
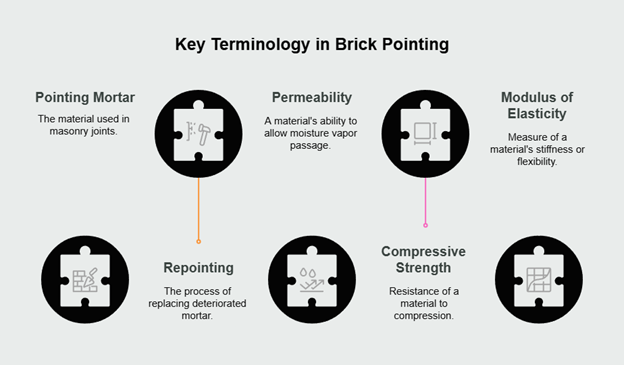
The foundation of informed material selection starts with understanding the basic types of pointing materials and their properties. Historically, pointing materials have evolved from simple lime-based mortars to today's diverse range of options including cement-based, lime-based, and hydraulic lime formulations.
Traditional lime mortars offered excellent breathability and flexibility but lacked durability in harsh conditions. Portland cement emerged in the late 19th century, providing superior strength but often proving too rigid for older structures.
Modern formulations now seek to balance these properties, with modified mixes that combine traditional benefits with modern performance.
Key Terminology
Mastering key terminology enables more productive conversations with contractors and suppliers:
- Pointing mortar: The material placed in masonry joints between bricks or stones
- Repointing: The process of removing deteriorated mortar and replacing it with new material
- Permeability: A material's ability to allow moisture vapor to pass through
- Compressive strength: A material's resistance to being compressed or crushed
- Modulus of elasticity: A measure of a material's stiffness or flexibility
These fundamentals provide the knowledge base required to evaluate more complex material characteristics and make appropriate selections for buildings in the Bronx environment.
Material Performance Characteristics Assessment
The performance of pointing materials depends on several critical factors that directly impact longevity and compatibility with existing structures. Property managers should evaluate these characteristics based on their building's specific needs rather than generic recommendations.
Flexibility and strength exist in constant tension—materials must be strong enough to maintain joint integrity but flexible enough to accommodate building movement. Rigid, high-strength materials may create stress points that damage historic brick, while overly soft materials may deteriorate quickly in exposed areas.
Permeability represents perhaps the most crucial performance characteristic. The pointing material must allow moisture to escape from masonry walls at an appropriate rate. In the Bronx's freeze-thaw climate, this becomes particularly important.
Materials that trap moisture within walls can lead to spalling, efflorescence, and accelerated deterioration during winter months.
Durability under environmental stress varies significantly between material types. The Bronx's urban environment, with its combination of moisture, pollution, and temperature fluctuations, creates challenging conditions for masonry materials. Materials must withstand these conditions while maintaining both functional and aesthetic integrity.
Comparative Analysis of Common Materials
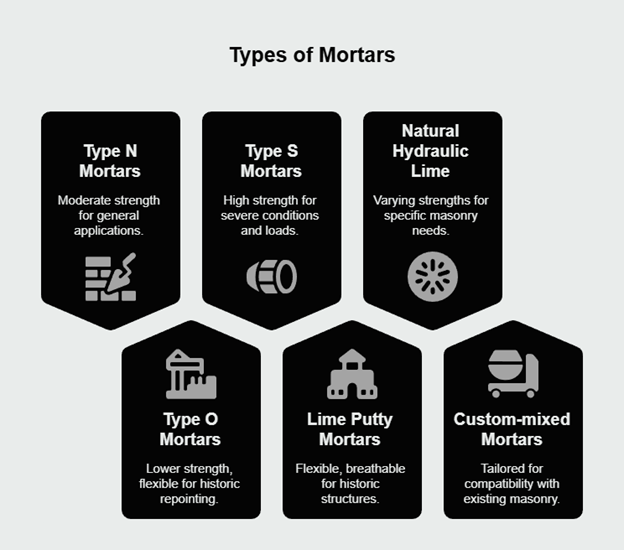
A comparative analysis of common material categories reveals important distinctions:
- Type N mortars (ASTM C270): Moderate strength, suitable for general applications above grade in protected exposures
- Type O mortars (ASTM C270): Lower strength, higher flexibility, often appropriate for repointing historic structures
- Type S mortars (ASTM C270): High compressive and bond strength (minimum 1800 psi), specifically designed for applications subject to high lateral loads, below-grade installations, or areas experiencing severe weather, seismic activity, or high winds
- Lime Putty mortars (non-hydraulic): Extremely flexible with excellent breathability, ideal for pre-1900 historic structures but requiring extended curing periods
- Natural Hydraulic Lime (NHL): Available in varying strengths (NHL 2, 3.5, and 5), offering graduated combinations of flexibility, permeability, and strength to match specific historic masonry requirements while setting without air exposure
- Custom-mixed mortars: Formulated for specific compatibility requirements with existing masonry
Each category offers different performance profiles that must align with both the technical requirements of the building and the operational needs of property management.
Compatibility Evaluation Framework
Compatibility between pointing materials and existing masonry is paramount to long-term performance. This evaluation goes beyond simply matching appearance—it requires understanding the physical and chemical properties of your building's original materials.
Begin by assessing the characteristics of existing masonry, including:
- Brick or stone type, age, and condition
- Original mortar composition (if determinable)
- Current moisture management patterns
- Previous repairs and their performance
- Areas of visible stress or deterioration
For Bronx buildings—many constructed in the late 19th and early 20th centuries—this assessment often reveals softer bricks that require more flexible pointing materials than modern construction.
Testing Methods
Compatibility testing provides objective data for material selection. Laboratory analysis offers the most definitive results through methods such as:
- Petrographic analysis to identify original mortar components and proportions
- Chemical analysis for precise binder-to-aggregate ratios
- Compressive strength testing to determine appropriate strength ranges
- Water absorption and permeability measurements
While field testing can provide valuable practical insights:
- Comparative water absorption between existing mortar and potential new materials
- Visual assessment of color and texture matching
- Sample installations in inconspicuous areas to evaluate performance over time
Avoiding Compatibility Failures
Common compatibility failures typically stem from mismatched properties. Modern cement-based materials applied to historic structures often create hard, impermeable joints that force moisture through the softer brick instead of the mortar joints.
This reverses the wall's designed moisture management system, accelerating brick deterioration and potentially causing spalling during freeze-thaw cycles common in Bronx winters.
Prevention strategies include thorough documentation of existing conditions, proper material testing before selection, and ongoing monitoring during the early stages of installation to catch potential issues before they become widespread problems.
Building-Specific Selection Criteria Development
Developing selection criteria specific to your building creates a decision-making framework that balances technical requirements with operational needs. This approach transforms a potentially overwhelming choice into a structured process.
Age and historical considerations significantly impact material selection. Buildings in the Bronx span multiple construction eras, each with distinct original materials and techniques. Older buildings (pre-1920s) generally require more traditional materials with higher lime content and greater flexibility. Structures from the mid-20th century may accommodate more modern formulations.
Practical Considerations
Use-case and occupancy factors create practical constraints around project scheduling and performance requirements.
Consider:
- Tenant disruption tolerance
- Seasonal occupancy patterns
- Building envelope performance expectations
- Maintenance access limitations
- Future renovation plans
Climate and exposure assessment is particularly relevant in the Bronx, where buildings face:
- Freeze-thaw cycles during winter months
- Urban pollution exposure
- Varying sun exposure based on building orientation
- Potential salt exposure from nearby roadways
- Wind-driven rain patterns specific to building location
Aesthetic and restoration requirements must balance historical authenticity with practical constraints. This includes:
- Color matching capabilities for different material types
- Texture and finishing techniques
- Aging characteristics over time
- Consistency across multiple project phases
- Regulatory or landmark requirements for historically significant structures
These criteria form the foundation of a documented selection process that supports both immediate project needs and long-term building maintenance planning.
Craftsmanship and Installation Considerations
Even the most appropriate material selection can fail without proper installation techniques. Craftsmanship plays a crucial role in the long-term performance of any brick pointing project. The expertise of the installation team often determines whether your material selection achieves its potential lifespan.
Critical installation factors include:
- Joint preparation: Complete removal of deteriorated mortar to proper depth (typically 2-2.5 times joint width) without damaging surrounding masonry
- Pre-wetting: Appropriate moisture levels in existing masonry before application
- Proper mixing: Consistent proportions and adequate mixing time for uniform material properties
- Application technique: Multi-pass installation with proper compaction to eliminate voids
- Tooling: Proper joint profile to shed water and match historical appearance
- Curing protocols: Temperature and humidity control during critical setting periods
- Weather limitations: Avoiding installation during extreme temperatures or precipitation
Quality Control Measures
Property managers should establish quality control measures including:
- Pre-installation meetings to review expectations and techniques
- Sample panels for approval before full-scale work
- Regular inspection points during the project
- Documentation of installation conditions
- Post-installation performance monitoring
Reputable contractors following the National Park Service Preservation Brief 2: Repointing Mortar Joints in Historic Masonry Buildings will prioritize these craftsmanship elements, recognizing that installation quality often determines overall project success regardless of material selection.
Decision-Making Tools and Documentation
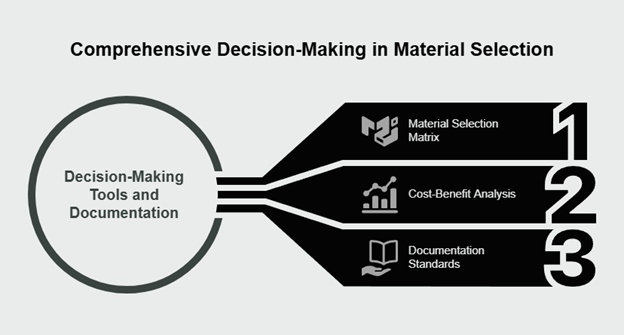
Translating selection criteria into actionable decisions requires structured tools and comprehensive documentation. A material selection matrix provides a systematic framework for evaluating options against your specific criteria.
The matrix should include:
- Material options under consideration
- Performance criteria with weighted importance factors
- Compatibility assessment results
- Installation considerations
- Budget impacts including initial and lifecycle costs
- Maintenance implications
- Contractor familiarity and experience
Cost-Benefit Analysis
A cost-benefit analysis framework helps justify higher initial investments when they deliver superior lifecycle performance. This analysis should consider:
- Initial material and installation costs
- Expected service life before required maintenance
- Potential impact on adjacent building materials
- Future accessibility costs for repairs
- Disruption costs to building operations
- Risk factors and their potential financial impacts
Documentation Standards
Documentation standards for brick pointing material selection decisions should include:
- Material specifications and sources (referencing ASTM C270 or other applicable standards)
- Compatibility test results
- Samples of selected materials
- Installation guidelines and quality control parameters
- Warranty information
- Maintenance recommendations
- Rationale for selections, particularly if deviating from common practices
This documentation becomes invaluable for future maintenance planning, providing critical context for subsequent work on the building envelope. It enables knowledge transfer between property management teams and ensures consistency in maintenance approaches across ownership transitions.
Conclusion
Material selection for brick pointing represents a critical decision point that impacts building performance, maintenance costs, and asset value preservation. By understanding material fundamentals, assessing performance characteristics, evaluating compatibility, developing building-specific criteria, and implementing structured decision tools, property managers can navigate this decision with confidence.
The process outlined provides a framework applicable to buildings throughout the Bronx, adaptable to specific age, construction, and use requirements. Thorough documentation of your selection process not only supports current project execution but establishes a valuable reference for future maintenance planning.
Remember that material selection is not merely a technical decision—it's a strategic one with long-term implications for your property management objectives and building asset value. Invest the time to make informed selections now, and your building will benefit from enhanced protection, reduced maintenance cycles, and improved performance for years to come.
Frequently Asked Questions (FAQs)
Q: What factors most significantly impact the long-term performance of pointing materials?
A: Material performance depends primarily on compatibility with existing masonry, appropriate water permeability characteristics, installation quality, and climate considerations. These factors interact differently depending on your building's specific construction, age, and location. Successful material selection requires evaluating these elements as an interconnected system rather than isolated variables. The financial implications of choosing inappropriate materials often manifest years later through accelerated deterioration, potential damage to the masonry units themselves, and significantly higher remediation costs.
Q: How should we balance higher material costs against potential longevity benefits?
A: This decision requires lifecycle cost analysis rather than initial expense comparison. Premium materials typically offer longer service intervals, reduced building envelope failures, and lower cumulative maintenance costs. Organizations should evaluate total ownership costs over a 20-30 year horizon, including installation labor, scaffolding/access costs for future work, and potential building damage risks. Cross-functional input from facilities, finance, and operations teams ensures comprehensive evaluation of both direct and indirect costs associated with different material quality tiers.
Q: What documentation should we maintain regarding material selection decisions?
A: Comprehensive documentation serves multiple organizational purposes beyond immediate project needs. Maintain detailed records of compatibility testing results, material specifications, mixing proportions, installation conditions, supplier information, and decision rationales. This information becomes invaluable for future maintenance cycles, troubleshooting any performance issues, warranty claims, and knowledge transfer during staff transitions. Implement a standardized documentation system that connects material selections to specific building sections and integrates with your broader asset management system.
Frequently Unasked Questions (FUQs)
Q: How do tenant lease structures and vacancy planning affect material selection decisions?
A: Organizations often overlook how lease structures and planned vacancy periods influence optimal material choices. Premium materials with longer installation time requirements may align better with planned vacancies or lease transitions, offsetting higher costs through reduced tenant disruption during future maintenance cycles. Consider how your lease structure affects maintenance timing flexibility and how material durability characteristics align with your portfolio strategy for the building. This alignment between material performance and business operations represents a strategic approach beyond purely technical considerations.
Q: What organizational knowledge gaps typically lead to suboptimal material selection decisions?
A: Many organizations lack cross-functional integration between technical, financial, and operational perspectives when making material selections. Facilities teams may focus exclusively on technical performance while disconnected from financial teams' capital planning horizons. This siloed approach often results in false economies where short-term budget constraints drive decisions that increase long-term costs. Developing interdepartmental evaluation frameworks and shared decision criteria significantly improves material selection outcomes and organizational resource allocation.
Q: How should material selection processes differ for buildings with different portfolio timeframes?
A: Organizations benefit from customizing their material selection approach based on long-term portfolio strategy. Buildings with different intended holding periods present different optimization challenges. For all properties, materials must maintain structural integrity and performance throughout the building's service life under management. However, the evaluation of premium materials with extended longevity benefits should consider the building's position in your portfolio timeline. This requires clear communication between asset management and maintenance teams about the strategic direction for each property. Developing tiered material selection protocols based on building performance requirements and maintenance planning horizons can optimize capital allocation across your entire portfolio while ensuring appropriate performance standards for each building's specific needs.
Disclaimer: This content is for informational purposes only and not intended as business advice. No business relationship is formed through this content. The information provided does not replace professional consultation. Please consult qualified business advisors for guidance specific to your organization's situation.
Ensure Lasting Results with Expert Brick Pointing
Choosing the right pointing material is key to preserving your building—and at City Suburb, we’ve been helping property managers across NYC do just that with expert craftsmanship and proven results.
Call us at 718-849-8999 to get trusted guidance and quality brick pointing tailored to your building’s needs.
Follow us for more masonry tips and project insights: Facebook | Instagram
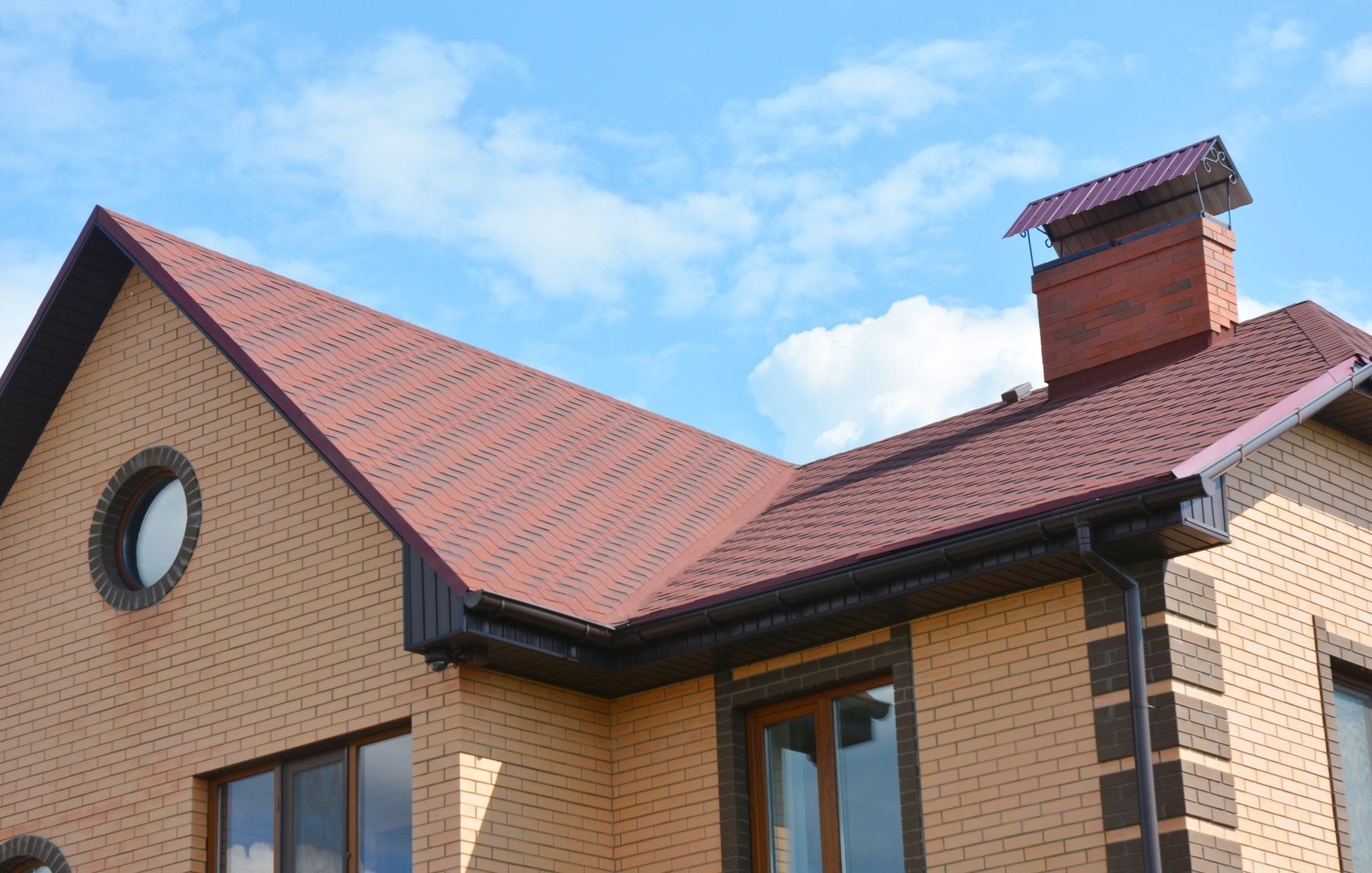
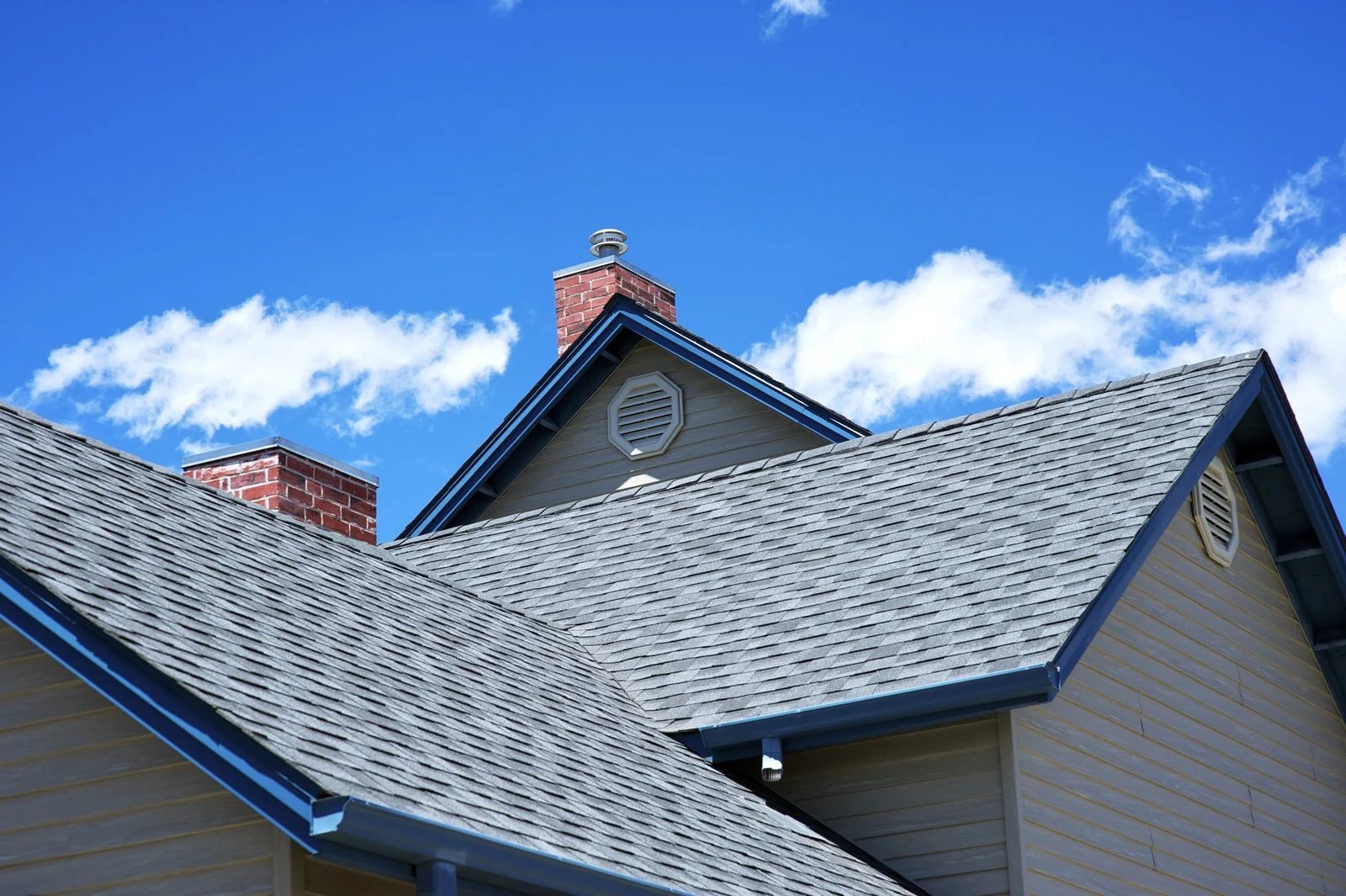
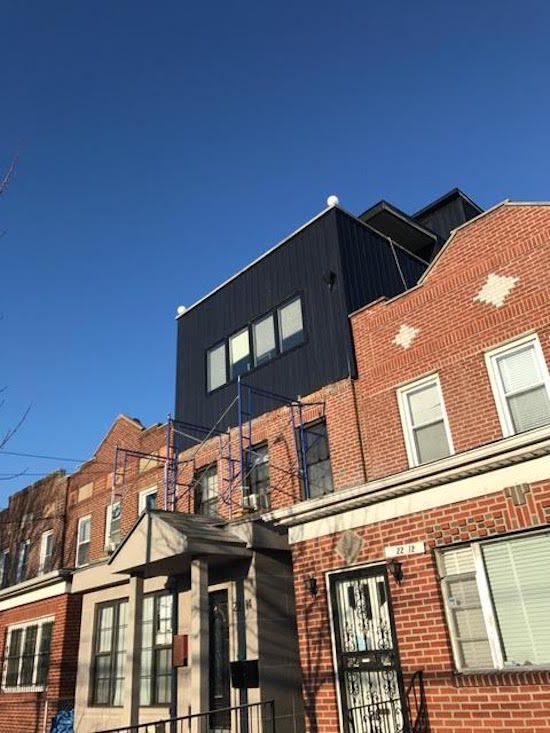
